Powering Progress: How Preventive Maintenance Can Revolutionize Industrial Facility Performance
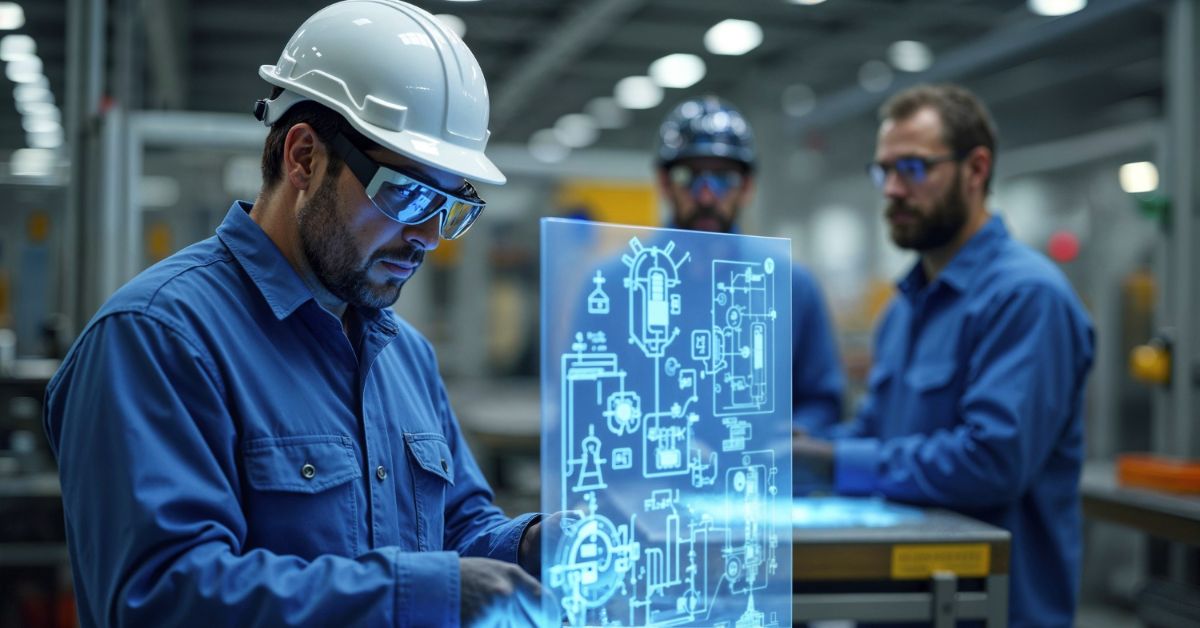
Why Preventive Maintenance Matters
In industrial environments, where the stakes are high and downtime can result in significant financial losses, adopting a proactive maintenance strategy is crucial for maintaining business vitality. Every hour that key systems stop working due to unexpected malfunctions doesn’t just stall production; it can also jeopardize supply chains, harm reputations, and inflate repair costs. That’s why organizations are shifting toward regular, structured maintenance activities, drawing inspiration from industry best practices and trusted resources like https://cbeuptime.com/ for insight into reducing downtime and boosting facility efficiency.
Preventive maintenance is fundamentally about anticipation and preparation. Rather than being caught off guard by equipment breakdowns, facilities leverage data and previous trends to plan their maintenance schedules with military precision.
Common Challenges in Industrial Facilities
Despite the clear advantages, industrial facilities often encounter significant barriers when implementing a comprehensive preventive maintenance plan. For many, the reality is a daily balancing act, juggling limited technical staff, stretching tight budgets, and nursing a backlog of urgent maintenance requests. Some facilities grapple with change resistance, where a “run-to-failure” mindset has persisted for years. Adding to the complexity, managers frequently face a patchwork of old and new equipment, each demanding separate service intervals and maintenance approaches.
The path forward starts by recognizing maintenance as an investment, not an expense. Facility decision-makers can identify critical assets that would cause the most significant disruptions if they failed and begin by focusing preventive efforts on those. Implementing digital maintenance reminders and investing in simple automation tools can ease the burden on technicians. Over time, demonstrating value through reduced downtime and better asset performance builds support across teams and gradually helps shift workplace culture to one where reliability is everyone’s priority.
Core Elements of an Effective Maintenance Plan
Designing a robust maintenance plan isn’t just about setting calendar reminders, as it involves creating an organized, actionable playbook for every asset under care. The process begins by cataloging all machinery and infrastructure, ensuring nothing is overlooked. Each item should be assigned a maintenance schedule based on manufacturer guidance, historical data, and observed performance trends within the facility.
A well-documented plan includes routine inspections, checklists tailored to each equipment type, and documentation protocols to record findings after every service. Organizations that implement structured preventive maintenance can achieve facility-wide energy improvements of up to 20 percent, resulting in significant monthly savings. The most resilient teams also log key repair events, capturing issues as they emerge and referencing these records during troubleshooting. This vigilant, process-driven approach minimizes surprises and provides a historical roadmap for future upgrades or audits.
The Role of Technology in Maintenance
The digital revolution is reshaping how industrial facilities approach their maintenance routines. Modern maintenance management systems (CMMS) and mobile applications provide operators with more visibility into workflows, allowing tasks to be assigned, tracked, and completed from mobile devices or computers. Internet of Things (IoT) sensors have further transformed the space, transmitting real-time performance data and triggering instant alerts the moment anomalies are detected, sometimes before personnel even notice a potential fault.
Predictive analytics, powered by these smart technologies, can estimate optimal servicing intervals and identify early warning signs much faster than traditional methods. This empowers facilities to move beyond fixed schedules, adopting data-driven maintenance that is tailored to each machine’s unique needs. The result: maintenance teams spend less time on unnecessary inspections and more time solving meaningful challenges, resulting in higher productivity and lower costs without sacrificing reliability.